SiFlieger (“Sicheres Fliegen senkrecht startender RPAs”) is a LuFo (Luftfahrtforschungsprogramm des Bundesministeriums für Wirtschaft und Energie ()) funded research project. Within this project the FSR investigates, how prognosis and health management (PHM) techniques can be utilized to generate an improved and dynamic safety assessment. The applicability of this method is demonstrated with an electromechanical actuator, which is part of a remotely piloted aircraft’s (RPA) control surface actuation system. http://www.bmwi.de
Diagnosis and Prognosis
To assess the current and future health status of this actuator a PHM algorithm is developed along to the OSA-CBM steps. From a data acquisition and a filtering process different features are extracted. From these features, smaller feature sets are selected which describe the degradation of the actuator’s parts. Thereby, it is possible to determine the health state, which is used as input for a prognosis step. The prognosis algorithm outputs the distribution of the remaining useful lifetime for maintenance planning and the consecutive system safety and availability determination.
The whole PHM process uses data-based methods. Therefore, an extensive data set of degradation curves is determined using the test rig.
This subtask focusses on:
- Data Manipulation ((Short-Time) Fourier Transform, Wavelet Analysis and Statistical Parameters e.g. Kurtosis, RMS…)
- Feature Selection (Cluster Analysis, Principal Component Analysis…)
- Health Assessment based on selected features
- Prognosis (Gaussian-Process-Regression, Neural Networks…)
System safety and availability
A central question of this project is how the prognosis results can be used to support the RPA’s operator in his decision-making (e.g. is the mission still safe or must be aborted). Therefore, a contingency awareness function is developed, which will aggregate all available information about the aircraft’s safety critical components as well as the current mission and generate an advice. The used information will include the results of a PHM system and thus considers the current and expected future health state of the monitored components.
This subtask focusses on:
- Reliability modelling (Fault Tree Analysis, Markov Models, failure rates and distributions)
- Failure mechanisms and their aggregation
- Uncertainty management (Monte-Carlo Simulation)
- Development of suitable evaluation metrics
- Evaluation of the developed methods on SiFliegeR’s test rig
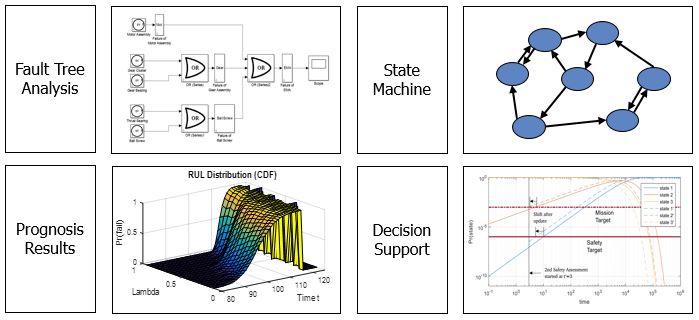
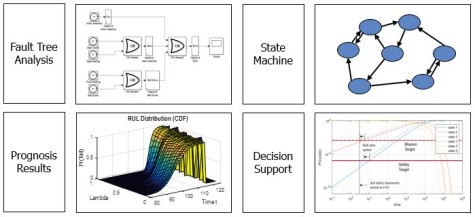
Evaluation (test rig)
The SiFliegeR test rig is designed to simulate and analyze the usage and degradation of a typical electromechanical actuator (EMA), as it is used in modern RPAs. Placed in the center of the test rig, the unit under test (EMA) is coupled to a torque motor. With this setup it is possible to apply dynamic loads and thus to simulate various flight conditions. The test rig is intended to evaluate and demonstrate the methods and algorithms, which are developed in this project.
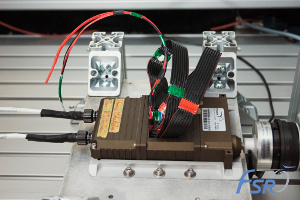
Servo Actuator – Unit Under Test
- Operating Voltage: Dual 28 VDC
- Rated Torque: 4 Nm
- Stall Torque: 7 Nm
- Speed @ Rated Torque: 135°/sec
- Max. Travel Angle: ± 150°
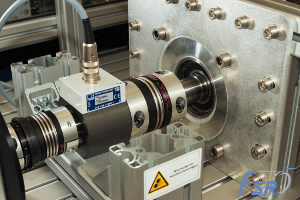
Torque Motor for Dynamic Load Application
- Operating Voltage: 400 VAC
- Rated Torque: 20 Nm
- Stall Torque: 25 Nm
- Speed @ Rated Torque: 2000 RPM
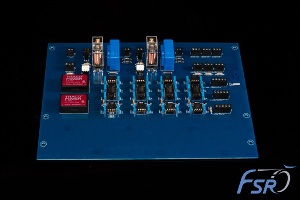
Sensors for PHM
- 16 Channel, 16 Bit, 100 kS/s/ch simultaneous A/D-converter
- Torque by HBM @ 50 Nm
- Vibration by KISTLER @ 50 g
- BLDC Phase Current Sensors by LEM @ 50 kHz
- Absolute Position Encoder 0.04 Degrees Resolution
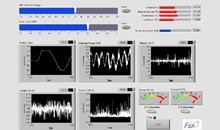
National Instruments for Experiment Control and Data Acquisition
- CompactRIO Real Time Computer with FPGA
- Customized user interface for experiment control
- Expandable hardware and software integration
- Use of hardware and software industry standards